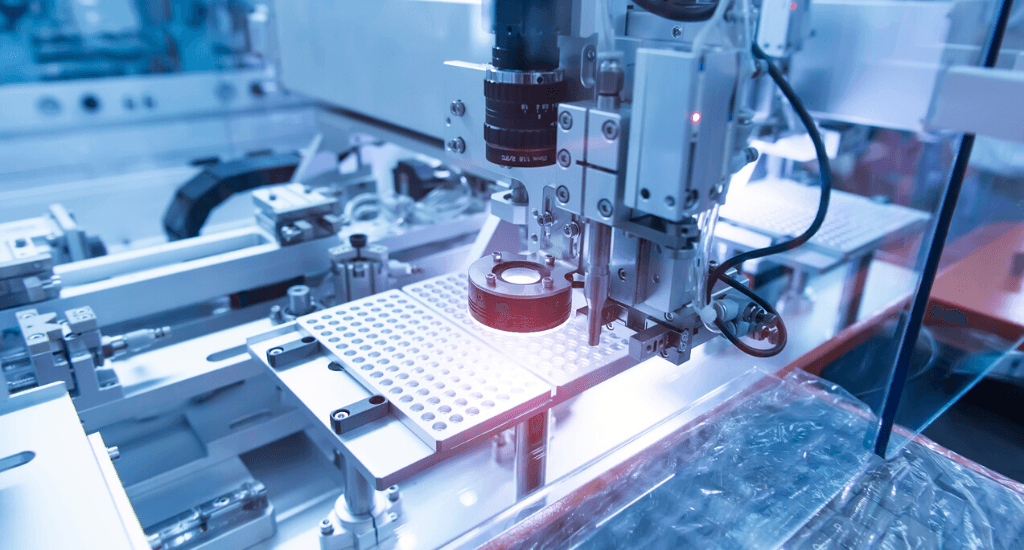
Today manufacturers must create high-quality products as efficiently and consistently as possible to remain competitive. With the increasing price of raw materials, skilled labor shortages, and rising competition, this can be difficult. Fortunately, machine learning and IoT technology are making efficiency and productivity gains a reality. According to McKinsey & Company, AI has the potential to create $1.2 trillion to $2 trillion in value for the manufacturing industry.
Manufacturers have access to a deluge of data like never before, such as images, sound frequencies, temperature, and more from sensor technology (smart manufacturing). Thanks to more accessibly-priced compute power, the manufacturing industry can make use of this data and reduce costs with machine learning and deep learning models. This is why manufacturers will benefit most from investing in people with data science and machine learning skills and the tools they need to develop innovative solutions that drive down costs. Here are four ways data scientists are generating value for manufacturers:
Demand Forecasting & Supply Chain Optimization
Throughout the supply chain, predictive analytics models are used to identify demand levels for different marketing strategies, sale prices, locations, and many other data points. They help predict consumer demand and consequently make recommendations to optimize the supply chain. Data scientists use predictive analytics models to anticipate the demand for specific products by using historical sales data, weather data, economic data, and more. Then, data from logistics management, transportation, and warehouse management can be used to optimize the supply chain.
After analyzing the gap between current and predicted inventory levels, data scientists create optimization models that help guide the exact flow of inventory from manufacturer to distribution centers and ultimately to customer-facing storefronts. This maintains an optimal balance between centralized and localized storage, minimizing unnecessary holding costs. Machine learning empowers manufacturers — and their logistics partners — to be more efficient and profitable. Data scientists constantly test different scenarios to ensure ideal inventory levels and improve brand reputation.
Quality Control
Image recognition and anomaly detection are types of machine learning algorithms that can quickly detect and eliminate faulty parts before they get into the manufacturing workflow. Parts manufacturers can capture images of each component as it comes off the assembly line, and automatically run those images through a machine learning model to identify any flaws.
Highly-accurate anomaly detection algorithms can detect issues down to a fraction of a millimeter. Predictive analytics can be used to evaluate whether a flawed part can be reworked or needs to be scrapped. Eliminating or re-working faulty parts at this point is far less costly than discovering and fixing them later in the manufacturing process, and reduces the risk of costly recalls. It also helps ensure customer safety, satisfaction and retention.
To implement an image recognition and analytics model, the manufacturer needs an accurate dataset containing hundreds or even thousands of parts images, each one tagged with information such as pass, fail, issue A/B/C, etc. The data scientist constructing the model must also have domain expertise regarding allowable tolerances and the potential performance and safety impact of various flaws.
Root Cause Analysis
When an issue arises at any point in the product lifecycle — whether it’s something found early in the manufacturing process or an issue affecting products already in consumers’ hands — organizations scramble to determine the exact cause and how to resolve it. The brand’s reputation (and possibly consumer safety) are at stake.
During the manufacturing phase, identifying the root cause(s) of an issue is a lengthy and painstaking process. Root cause analysis uses massive amounts of testing data, sensor measurements, manufacturer parameters and more. Performed with traditional methods, it’s also incredibly hard.
Machine learning techniques can vastly accelerate root cause analysis and speed resolution. Anomaly detection algorithms can analyze vast amounts of sensor and system data efficiently. And they can perform this analysis using additional data types and in far greater quantities than traditional methods can handle.
For example, during the manufacturing phase, the use of image data as an input for root cause analysis helps organizations correlate failure modes to possible flaws in the underlying manufacturing procedures. If issues arise once products are in the hands of consumers, text recognition and natural language processing on social media enable the inclusion of these notes in the analysis process. Each of these approaches can reveal very specific root causes months faster than traditional analysis — and oftentimes diagnose issues that may not be uncovered any other way.
Predictive Maintenance
Machine learning can provide far more precise and — importantly — evolving maintenance recommendations. Algorithms process historical machine data and sensor data to predict when a machine is likely to fail and trigger alerts, empowering manufacturers to provide preventative maintenance just in time, avoiding the cost of downtime.
Rather than a static maintenance schedule that gets updated a few times a year, a predictive analytics model can continue to learn from thousands of performance data points collected from manufacturing plants, suppliers, service providers, and even products in use. The model adapts to changing conditions and new performance information, updating the maintenance schedule accordingly
Predictive maintenance with ML helps manufacturers plan and budget for new equipment or new parts as machines reach end-of-life. It can also help reduce waste. For example, when a machine breaks down or performs suboptimally, raw materials are often wasted in the process. Predictive analytics also helps improve compliance with recommended maintenance and can keep manufacturing systems working at optimal performance levels — protecting yield, helping to ensure quality and safety, and ultimately saving time and money. According to McKinsey & Company, predictive maintenance typically reduces machine downtime by 30-50% and increases machine life by 20-40%.
Open-Source Technologies Provide Innovative Solutions
With the right skill set, data scientists in the manufacturing industry can provide a strategic advantage by implementing the use cases discussed here using Python and cutting edge open-source libraries like TensorFlow, scikit-learn, and scikit-image. For this reason, many manufacturing organizations would realize greater value from an enterprise machine learning platform that incorporates open-source libraries and tools rather than a point solution designed for a single use case.